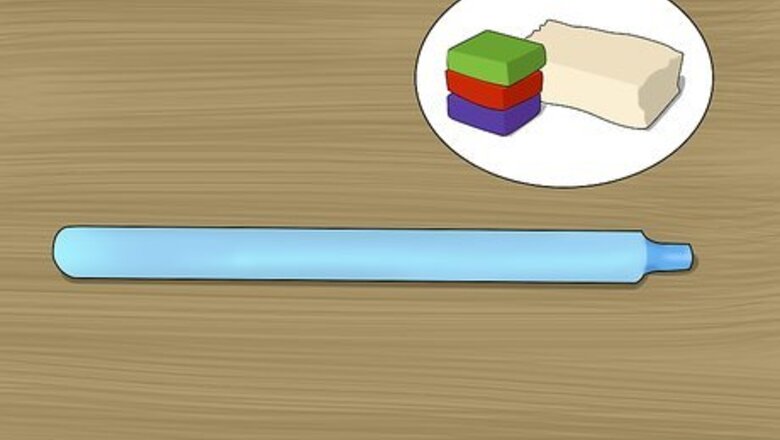
views
Quick and Easy Pen Methods
Shape a pen with polymer clay. Take out a pen's ink cartridge and cut a bamboo skewer to the same length. Wipe the skewer with petroleum jelly and use it to pierce a small ball of polymer clay. Roll out the clay until it extends along the whole skewer, seal it over one end, and bake according to clay's label instructions. Let cool 5–10 minutes, remove the skewer, then glue in the ink cartridge once the clay has cooled completely.
Use a piece of cane. A thin piece of bamboo is ideal, but any sturdy hollow cane will do. Cut off a cane segment underneath one joint, and just below the next. Drop an ink cartridge from an ordinary pen into the hollow end. Gradually make an angled cut into the solid end, until you can poke through with the ink cartridge tip. Seal the end with clay or putty to prevent ink leaking out. If the cartridge is too loose, hold it in with strong glue. If it's too long, hold it in place with tape.
Make a quill pen. Choose a large tail feather, and trim away enough feathers to comfortably hold the tip. Sand the tip smooth, then cut it away at a steep angle. To let the quill pick up ink, cut a slit from the tip inward, and chop off the extreme tip to make a flat edge. For best results, before you begin cutting, soak the feather in hot water until it bends easily, then harden it again in hot sand.
Making a Quality Pen
Purchase a pen kit. You'll most likely have to place an online order, as these are difficult to find even in craft stores. These include the ink cartridge and metal pieces. See the Things You'll Need section below for additional tools before you buy. The same source may be able to sell you those tools. This guide will work for any type of pen kit. Rollerball pens are slightly easier to assemble, but twist pen kits are usually the cheapest option.
Cut or purchase a pen blank. A pen blank is just a rectangular block with a hole drilled through the center, usually made from wood or Corian. You can practice on homemade scrap lumber blanks, then move on to pre-cut blanks with more attractive wood and "stabilized" treatment for a better fit. Line up the two brass tubes from your pen kit. Cut the blank a bit longer than this length. The other dimensions don't matter, as long as the blank is significantly larger than the desired pen size. A 5" x ½" x ½" (12.75 x 1.25 x 1.25 cm) blank should fit most pen kits.
Saw the blank apart. Line up the brass tubes next to your blank. Cut the blank into segments, each one slightly longer than a single brass tube. Most pen kits come with two brass tubes, but some use three. These may be different lengths, so use a different tube for each measurement. Draw a pencil line across the blanks so you can easily line up the grain.
Drill the pen blank. If you cut your own blank, hold each part in a drill press and drill through the center. The drill bit must match the outer diameter of the brass tubes in your pen kit. Drill slowly, in ½" (1.25 cm) increments, to avoid fracturing the material. Set the drill press' depth stop so the point just barely touches the opposite side. If it emerges fully, it will often "blow out" the whole blank, making you start again. Saw off the tip of the blank so the hole goes straight through. The most common sizes are 7mm (roughly J bit or 9/32") and 8mm (roughly O or 5/16"). If using imperial drill bits, you may want to test on scrap wood first to find the best fit. A slightly loose fit should turn out fine if you use extra glue.
Sand and glue in the brass tubes. Scuff the exterior of the brass tubes with rough sandpaper, about 120 grit. Optionally, plug the end with Play-Do or dental wax to avoid getting glue inside the tube. Apply glue and stick each brass tube into the blank of the same length. Wear gloves to minimize cleanup. Cyanoacrylate (CA) glue and 5-minute epoxy are popular choices. If you use polyurethane glue, wait until the final stage, when you're ready to assemble. This glue foams up as it cures, which can ruin the fit. (This is a possibility with all glues, but most pen makers prefer the convenience of gluing at this stage instead of leaving the tubes loose.)
Square the ends with a pen mill. Wait for the glue to cure, according to the glue's label instructions. Fit the pen mill rod into one of the tubes, and turn clockwise so the cutting edge squares the end. Repeat with each end of each blank, until every surface is flush with the end of the brass tube. Now's a good time to check the inside of the tubes for glue. Scrape it out using any tool. You can use a sanding jig instead, but it may take quite a bit of setup.
Mount blanks and bushings on a mandrel. Line up the pen blanks in the order they fit together, on the mandrel rod. Place a bushing in between them, and another bushing on either end. Fit the two ends of the mandrel to hold the pen in place. Check the kit instructions for recommended bushing size. If you really don't want to buy the pen mandrel you can mount each blank separately on a 60º live center instead. Shaping each piece separately will be much harder for a beginner, however.
Turn the pen on the lathe. Mount the mandrel onto your lathe. Shape the blank down to the diameter of the bushings, using gouges, skews, or any other lathe turning tools. Stop the lathe after the initial rough shaping, and loosen the mandrel nut and tailstock before you continue. These usually tighten during turning, which can lead to misshapen pens. Continue turning until you've achieved any shape you like. If you don't have a lathe, mount a sanding drum onto your drill press and hold the blank against it. You'll have much less control, but no one wants to buy a $300 lathe for a $2 pen.
Sand off tool marks. Remove the pen from the lathe. Sand the blanks with dry, 220 grit sandpaper. Repeat with 320, 400, and 600 grit to get a progressively smoother surface. There are plenty of variations on this exact sanding process, so don't feel that you have to use these exact grits. High-quality pens may be sanded up to 1200 grit at this stage, using mesh abrasive cloths.
Apply a finish and sand again. You can use any film finish, lacquer, or wood polish to give the pen a glossy, protective coating. Complete the blank by wetting it and sanding with finer grit sandpaper. Try polishing with 400 grit, 600, 800, 1200, 1500, 1800, 2400, 3200, 3600, and 4000 (using abrasive meshes for the highest grits). This can get a little tedious, but this is the bare minimum of sanding most pen-makers use. Some go as high as 12,000. Rub on paste wax for a shinier pen.
Assemble the pen. Your pen kit should include instructions for which pen components attach to which blanks. Use a pen assembly press or a simple bench vise to press on each metal component. Once all parts are firmly pressed on, your pen is complete. Here's a typical process for a twisting pen: Press the pen cap into the upper brass tube. Press the twisting mechanism into the lower tube. Before you press, lay the mechanism next to the blank, and twist to extend the tip. Note how far you'll have to press it in order for the tip to just barely protrude. Press the pen clip and cap onto the upper blank.
Comments
0 comment