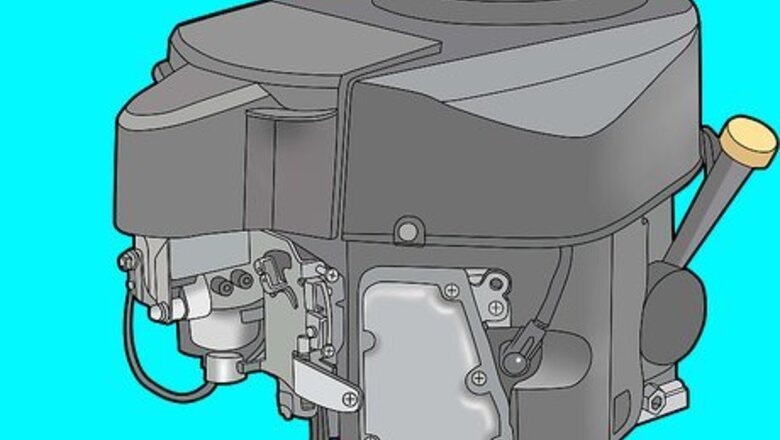
views
Obtain the Main Power Pieces
Acquire an engine. The required engine size is dependent on the amount of power that the generator will need to supply. A good rule of thumb for a useful, compact generator is to choose an engine in the range of 5 to 10 horsepower. Note that most engines rate their horsepower at a speed of 3,600 rotations per minute (RPM). These motors are about the size of lawn mower engines, and are typically available at lawn equipment stores, industrial supply shops or power equipment outlets.
Choose an AC generator head. This head will use an internal magnet to create electricity when the shaft mounted magnet is spun by the external engine. For most applications, output levels of 2,500 to 5,000 watts is suitable. In sizing the head, use the specification of the manufacturer to determine the engine size needed to drive that head. As a rough estimate, a generator can produce about 900 (749 watts per horsepower is the actual conversion) watts per input horsepower. Heads are available through industrial supply outlets and industrial equipment catalogs.
Select a 12 volt DC alternator. This alternator will generate 12 volts DC when the shaft is driven by the external engine. The alternator chosen must have a built-in voltage regulator. A 500 watt alternator is typically sufficient, and would require about another horsepower from the chosen engine. Alternators are widely available at auto parts suppliers.
Connect the Main Power Pieces
Fabricate a mounting plate. This mounting plate can be made of any sturdy material that can withstand the vibration of the gasoline engine. The 3 main power pieces (engine, generator head and alternator) must be mounted so that their shafts are parallel and the shaft attachment areas for drive pulleys are in the same plane. Mounting holes and mounting hole patterns must be derived from the manufacturer data for each of the 3 major power pieces.
Mount the pulleys. A pulley must be mounted to the engine shaft to belt drive the pulleys that will come already installed on the generator head and the alternator. This pulley size must be chosen so that when the engine is rotating at the nominal running speed given by the manufacturer, the belts will scale this up or down to the pulleys of the generator head and the alternator. Choose the scaling so that the generator head and the alternator are running at the rated speed indicated on the manufacturer data sheet. In most typical generators, this will result in an engine pulley of 5 to 10 inches (125 to 250 mm). Pulleys are available at industrial supply stores and through equipment supplier catalogs.
Run the belt or belts. The design of the generator may need different pulleys on the engine to apply proper shaft speed to the generator head and the alternator, or this may be workable with 1 engine pulley and 1 belt. Run the belt over the pulleys and make sure that they are taught. Slotting the mounting holes of the engine will provide good adjustment to achieve this. A V belt is preferable to a standard belt as it will have less tendency to slip. Belts may be acquired from the outlet that supplied the pulleys.
Mount the gasoline tank to the mounting plate.
Reconnect the gasoline supply. Fill the gasoline tank and place the fuel feed lines to the engine.
Comments
0 comment